- Venjakob
- Surface Pretreatment
- Surface Activation
Surface activation for improving wettability
Optimal pretreatment thanks to surface activation
High-quality surface activation is often a must to ensure optimal coating or painting of components, and modern surface pretreatment systems have long been a part of the Venjakob product range. We’ll be happy to explain why surface activation is so important for the success and quality of subsequent surface processing.
Many materials don’t have the necessary surface tension for further processing such as bonding and coating. Potential reasons include surface imperfections resulting from flaws or pores or possibly the chemical composition of the substrate, which may result in substance or processing aid diffusion on the component surface, ultimately leading to nonpolar (low-energy) surfaces. Activation, which refers to the modification of the component’s top molecular layer, can convert these nonpolar (low-energy) surfaces into polar (high-energy) surfaces, making these activated surfaces more wettable for improved coating.
FLAME PRETREATMENT
Plastic workpieces can be flame-treated with a gas burner prior to coating to improve the feel. Rather than being a form of heat treatment, flame treatment relies solely on the chemical effect of the gas flame.
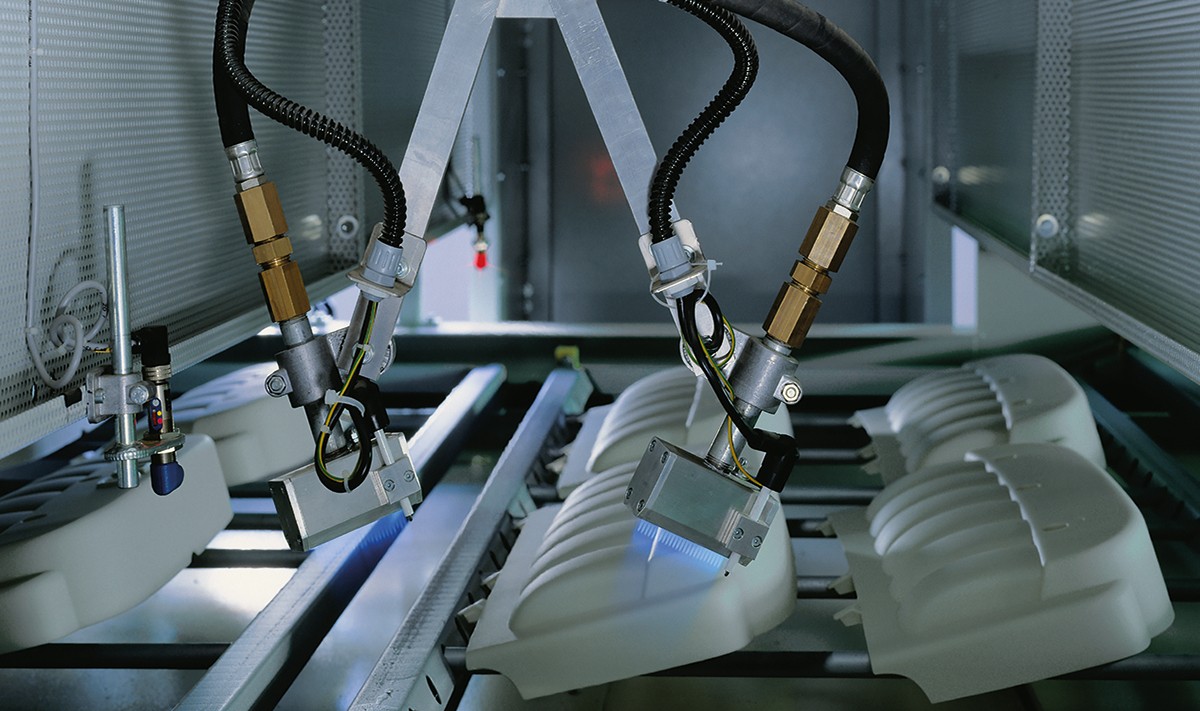
FLAME PYROLYSIS
For years now, flame treatment has been a common pretreatment process for increasing surface adhesion and thus absorption of adhesives, coatings, and print media.
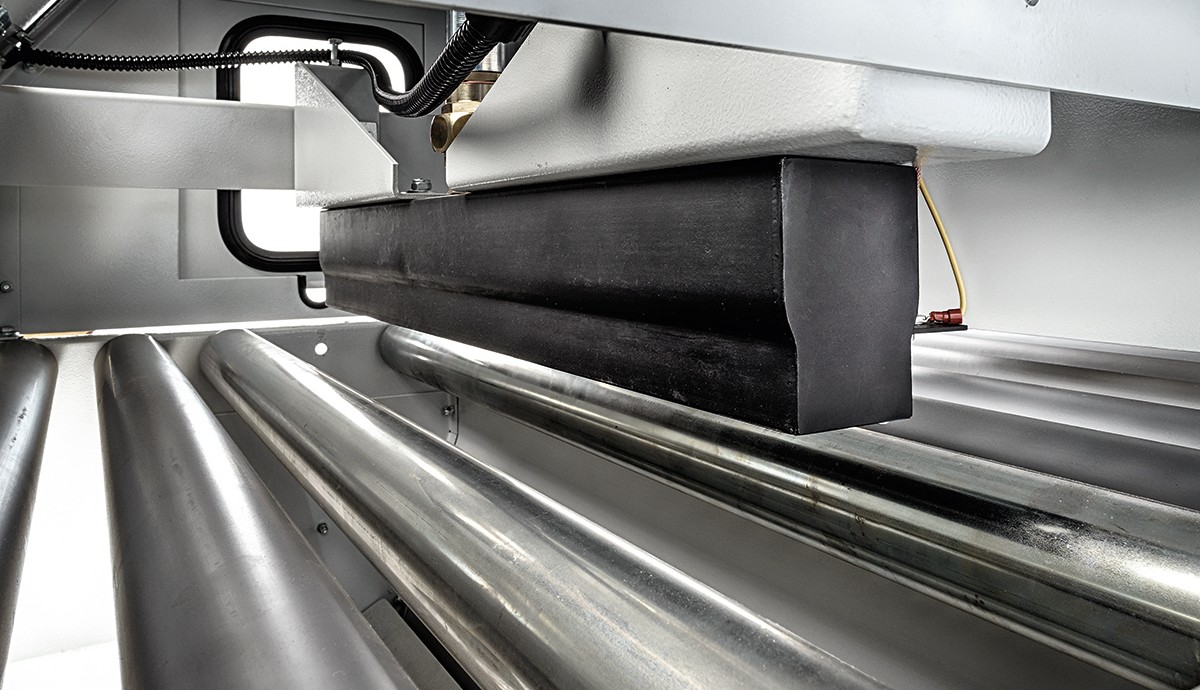
PLASMA ACTIVATION
Plasma activation ensures especially efficient surface modification for plastic, metal, composites, and more.
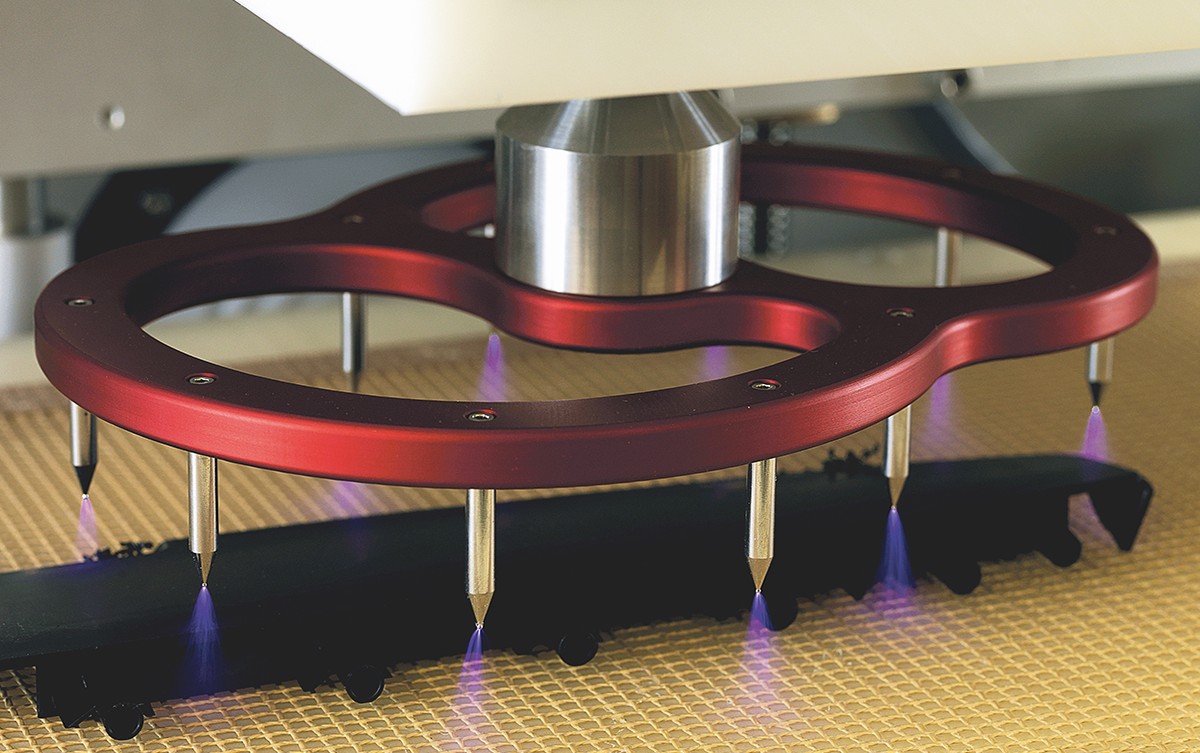
Your contact person